Zregenerowany nie znaczy gorszy fakty i mity o siłownikach po naprawie
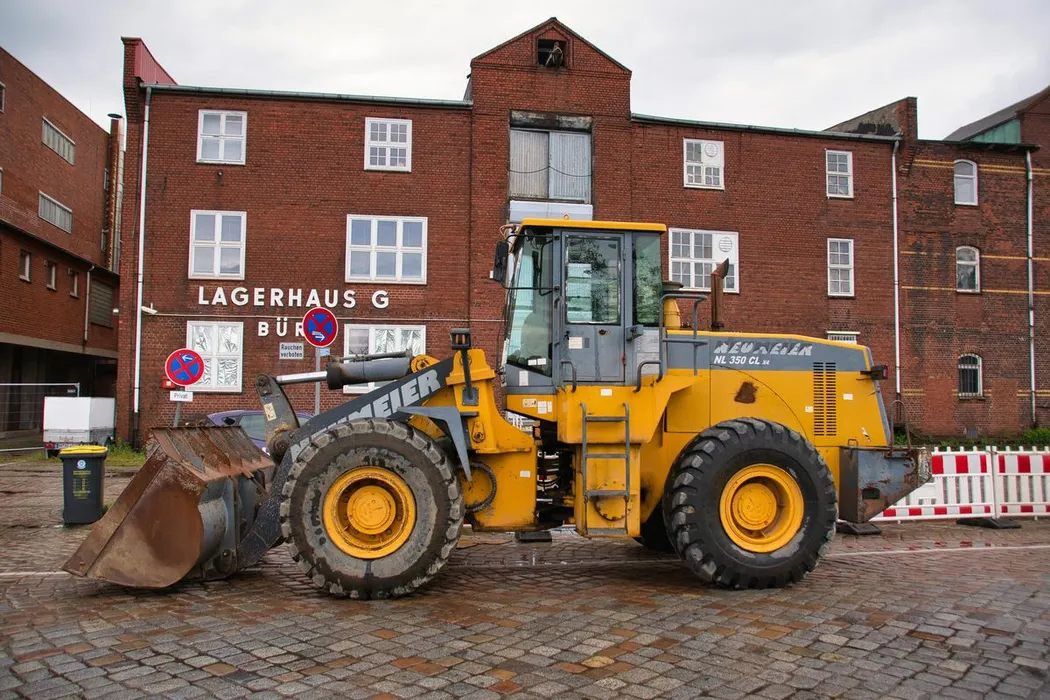
Regeneracja siłowników hydraulicznych w przemyśle ciężkim przechodzi prawdziwą rewolucję. Badania wskazują, że profesjonalnie odnowiony siłownik może osiągać parametry pracy identyczne jak fabrycznie nowy, a w niektórych przypadkach nawet przewyższać tanie zamienniki z rynku. Mimo tych faktów, wśród inżynierów utrzymania ruchu wciąż pokutuje przekonanie o tymczasowości tego rozwiązania. Przyjrzyjmy się bliżej technologii regeneracji siłowników hydraulicznych oraz jej rzeczywistym zaletom i ograniczeniom.
Dlaczego regeneracja siłowników hydraulicznych to realna alternatywa dla nowych części?
Siłowniki hydrauliczne, mimo solidnej konstrukcji, ulegają naturalnemu zużyciu. Najczęściej uszkodzeniu podlegają elementy uszczelniające, powierzchnie tłoczysk oraz tuleje cylindrowe. Diagnostyka laserowa pozwala dziś precyzyjnie określić, które komponenty wymagają wymiany, a które regeneracji. Profesjonalna obróbka tłoczysk poprzez nałożenie nowych powłok metodą napawania plazmowego lub natryskiwania HVOF (High Velocity Oxygen Fuel) przywraca im pierwotne wymiary, ale także często zwiększa odporność na korozję i ścieranie. Regenerowane tuleje cylindrowe poddawane są procesowi honowania, który nadaje powierzchni idealną gładkość, zapewniając lepsze parametry pracy niż niektóre fabrycznie nowe elementy niższej jakości.
Różnice cenowe między nowymi a regenerowanymi siłownikami są zauważalne. Przykładowo, regeneracja siłowników hydraulicznych w koparce klasy 20-30 ton to koszt około 30-45% ceny nowego oryginalnego elementu. W przypadku maszyn przemysłowych o większych gabarytach oszczędności mogą sięgać nawet 60-70%. Dla przedsiębiorstwa posiadającego flotę 10 maszyn budowlanych oznacza to potencjalne oszczędności rzędu kilkudziesięciu tysięcy złotych rocznie.
Jak wygląda profesjonalna regeneracja krok po kroku?
- Proces profesjonalnej regeneracji rozpoczyna się od kompleksowej diagnostyki. Siłownik poddawany jest badaniu na specjalistycznych stanowiskach testowych, gdzie sprawdza się szczelność, geometrię oraz stan powierzchni roboczych. Pomiary mikrometryczne z dokładnością do 0,001 mm pozwalają określić rzeczywisty stan zużycia elementów.
- Kolejnym etapem jest demontaż i czyszczenie wszystkich komponentów. Tutaj stosuje się zarówno metody mechaniczne, jak i chemiczne. Po dokładnym oczyszczeniu następuje regeneracja uszkodzonych elementów. Tłoczysko z wżerami korozyjnymi lub zarysowaniami poddawane jest obróbce skrawaniem, a następnie napawaniu lub chromowaniu technicznemu. Dzięki specjalistycznym obrabiarkom CNC możliwe jest przywrócenie idealnej geometrii z tolerancją na poziomie kilku mikrometrów.
- Tulejowanie cylindra to proces polegający na osadzeniu nowej tulei wewnątrz zużytego cylindra. Następnie wykonuje się honowanie - obróbkę wykańczającą, która nadaje wewnętrznej powierzchni odpowiednią strukturę geometryczną. Właściwie wykonany proces honowania zapewnia idealne przyleganie uszczelnień oraz minimalizuje tarcie podczas pracy siłownika.
- Montaż odbywa się w warunkach kontrolowanej czystości. Używa się nowych zestawów uszczelnień, często o podwyższonych parametrach w stosunku do oryginalnych. Kompletny siłownik poddawany jest rygorystycznym testom końcowym. Sprawdza się szczelność statyczną przy ciśnieniu przekraczającym o 20-30% nominalne ciśnienie robocze oraz przeprowadza próby dynamiczne symulujące rzeczywiste warunki pracy. Każdy parametr zostaje udokumentowany w protokole powykonawczym.
Fakty kontra mity najczęstsze nieporozumienia wokół siłowników po naprawie
Popularny mit głosi, że siłownik po regeneracji ma niższą wytrzymałość niż fabrycznie nowy. Badania przeprowadzone przez Politechnikę Wrocławską wykazały, że prawidłowo zregenerowany siłownik z zastosowaniem nowoczesnych technologii napawania i obróbki powierzchniowej może wykazywać odporność na ścieranie wyższą o 15-20% w porównaniu do standardowych rozwiązań fabrycznych. Wynika to z możliwości zastosowania materiałów o podwyższonych parametrach, niedostępnych w masowej produkcji ze względu na koszty.
Kolejne nieporozumienie dotyczy zakresu regeneracji. Wielu użytkowników błędnie zakłada, że każda regeneracja oznacza kompletną odbudowę siłownika. W rzeczywistości profesjonalne serwisy jak Luchs Polska, stosują podejście selektywne - wymieniają lub regenerują tylko te elementy, które rzeczywiście tego wymagają. Dzięki temu proces jest bardziej ekonomiczny i ekologiczny.
Wiele firm produkcyjnych celowo zniechęca do regeneracji, promując wyłącznie wymianę na nowe części. Praktyka ta wynika głównie z modelu biznesowego opartego na sprzedaży części zamiennych. Producenci rzadko informują, że większość siłowników projektowana jest z myślą o możliwości wielokrotnej regeneracji. Przykładowo, cylinder siłownika w maszynie budowlanej może przejść zazwyczaj 3-4 pełne cykle regeneracji bez utraty parametrów.
Regeneracja siłowników hydraulicznych przestaje być postrzegana jako rozwiązanie tymczasowe czy awaryjne. Profesjonalnie przeprowadzony proces odnowy zapewnia parametry pracy porównywalne z nowymi elementami, często przy dużo niższych kosztach. Kluczem do sukcesu pozostaje właściwa diagnoza oraz świadomy wybór specjalistycznego warsztatu dysponującego odpowiednią technologią. Pamiętajmy jednak, że regeneracja ma swoje techniczne i ekonomiczne granice. Umiejętność rozpoznania sytuacji, w których lepiej zainwestować w nowy siłownik, świadczy o profesjonalnym podejściu do zarządzania utrzymaniem ruchu.
Autor: Artykuł sponsorowany